Understanding Industrial Blower Design
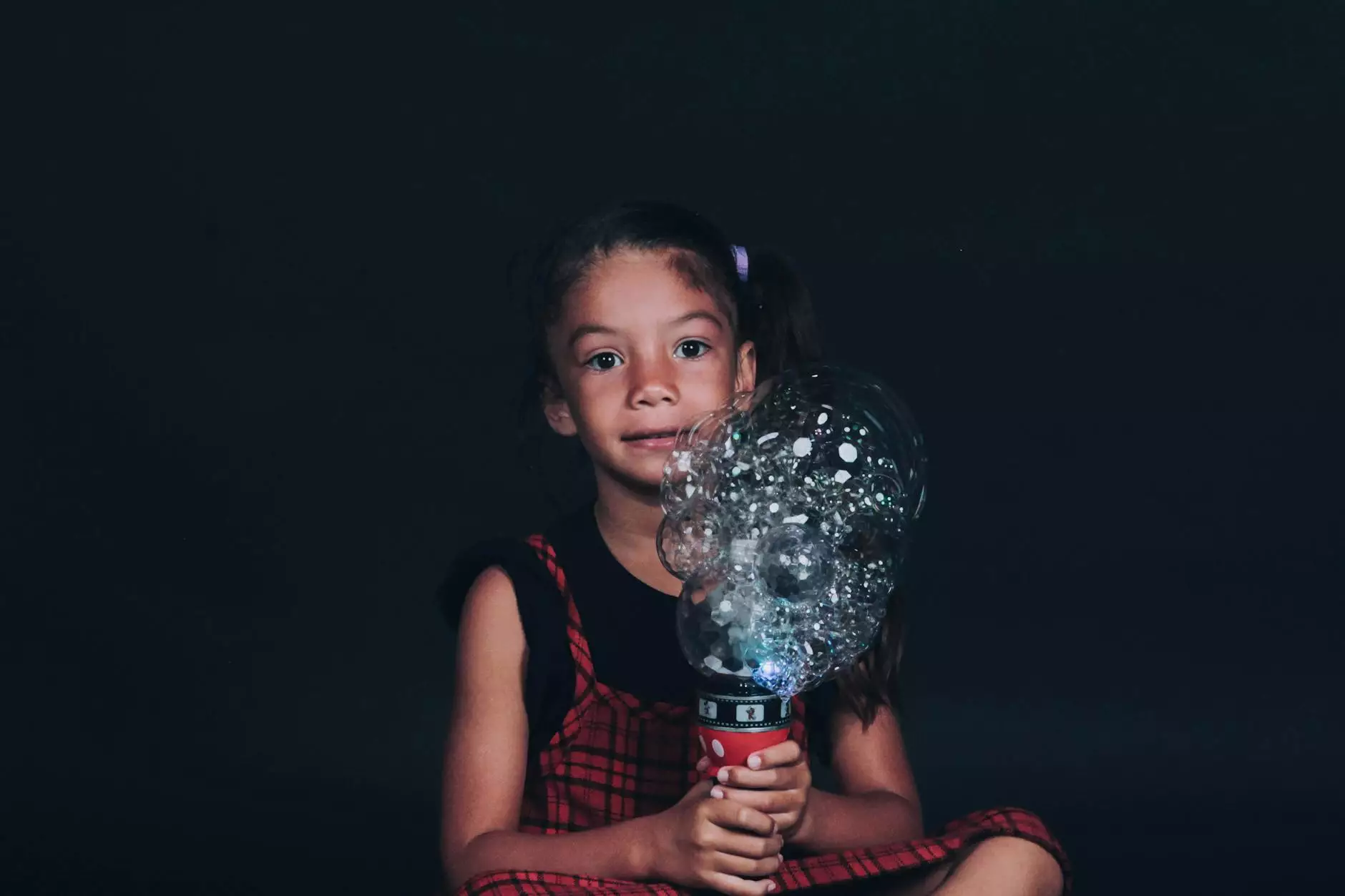
Industrial blowers are crucial components in many manufacturing and processing applications. They are designed to move air or gases in a controlled manner, which can significantly enhance operational efficiency. This article delves into the intricacies of industrial blower design, offering insights into its functionality, key considerations, innovative technologies, and application areas.
The Importance of Industrial Blow Systems
In various industries, efficient air movement is paramount. The role of industrial blowers is critical; they help maintain air quality, control temperature, and ensure proper ventilation. From manufacturing plants to agricultural operations, industrial blowers support essential processes that drive productivity.
Applications of Industrial Blowers
The applications of industrial blowers are vast and varied. Here are some key sectors where they are deployed:
- Manufacturing: In the production line, blowers are used for drying surfaces and cooling machinery.
- Mining: They assist in dust control and ventilation in mines, enhancing worker safety.
- Environmental Control: Industrial blowers are used in air pollution control systems and waste management.
- Agriculture: In poultry and livestock operations, blowers help regulate temperatures and humidity levels.
- HVAC Systems: They play a fundamental role in heating, ventilation, and air conditioning systems.
Core Components of Industrial Blower Design
The effectiveness of an industrial blower largely depends on its design. High-quality blowers are composed of several integral parts:
1. Blower Wheel
The blower wheel is pivotal to the performance of any blower. It can be constructed from various materials, such as aluminum or plastic, and is designed to provide optimal airflow. The choice of wheel design—centrifugal or positive displacement—affects the volume and pressure of the airflow.
2. Motor
The motor drives the blower and can significantly influence its energy consumption. Selecting a high-efficiency motor type (e.g., IEC, NEMA) is crucial for reducing operational costs.
3. Housing
The housing encases the blower's internal components. It should be crafted from sturdy materials to withstand corrosion and wear. The design of the housing is essential for minimizing noise and vibration during operation.
4. Inlet and Outlet Channels
Properly designed inlet and outlet channels enhance airflow direction and efficiency. These channels must be optimized to reduce turbulence and pressure losses.
Design Considerations for Optimal Performance
Effective industrial blower design necessitates a thorough understanding of several factors:
1. Airflow Requirements
Understanding the required airflow rate is essential. This involves assessing the volume of air needed for specific applications and calculating the pressure drop across the system.
2. Noise Control
Noise pollution can be a significant concern in industrial environments. To combat this, advanced design techniques such as sound dampening materials and strategic placement of blowers can be employed.
3. Energy Efficiency
As businesses strive to cut costs, integrating energy-efficient components is vital. The selection of motors, impellers, and overall blower architecture can hugely impact energy consumption.
4. Maintenance Requirements
An effective design should also consider ease of maintenance. Products that require minimal maintenance or offer predictive maintenance options tend to be favored in industrial settings.
Advancements in Industrial Blower Technologies
Advancements in technology continue to transform industrial blower design. The following innovations are leading the charge:
1. Smart Blower Technology
Smart technology has made its way into many industrial applications. Blowers can now feature IoT capabilities, allowing for remote monitoring and management. Data analytics can help predict maintenance needs before issues arise.
2. Variable Speed Drives
By incorporating variable speed drives (VSD), blowers can adjust their performance based on real-time demands rather than operating at a constant speed, yielding substantial energy savings.
3. Innovative Materials
The development of lightweight and corrosion-resistant materials has improved durability and efficiency in blower design, leading to longer lifespans and reduced operational costs.
Choosing the Right Industrial Blower
Selecting the appropriate industrial blower involves careful consideration of numerous factors:
1. Flow and Pressure Requirements
Every application has specific flow and pressure needs. Thorough analysis must be conducted to ascertain the precise requirements.
2. Physical Space Constraints
The dimensions and layout of the site affect the blower choice. Compact designs may be necessary for applications with restricted space.
3. Environmental Conditions
Blowers must be designed to withstand the environmental conditions they will face, such as temperature extremes and humidity.
4. Cost Considerations
While initial cost is critical, evaluating the expected lifecycle cost is essential. Choosing a less expensive option may lead to higher energy costs and increased maintenance over time.
Future Trends in Industrial Blower Design
The future of industrial blower design is set to be influenced by trends focused on sustainability and digitalization.
1. Sustainability Practices
As industries move towards greener practices, blowers that maximize efficiency while minimizing energy use will be in high demand. Recyclable materials and designs that facilitate energy recovery will become standard.
2. Digital Twins
The concept of digital twins offers the possibility of creating an accurate model of the blower system. This model can be used for simulation, performance optimization, and predictive maintenance strategies.
3. Integration with Renewable Energy Sources
As more factories aim to reduce their carbon footprints, the integration of industrial blowers with renewable energy sources, such as solar panels and wind turbines, is likely to increase.
Conclusion
An effective industrial blower design promotes enhanced productivity and energy efficiency across various sectors. Businesses looking to remain competitive must invest in cutting-edge blower technologies and consider design principles that align with their operational goals. By understanding the intricacies of blower design, companies can select systems that not only meet their current needs but also adapt to future challenges.
For more information on tailored industrial blower solutions that fit your unique requirements, visit TMM today!