Understanding Die Casting Components Manufacturers
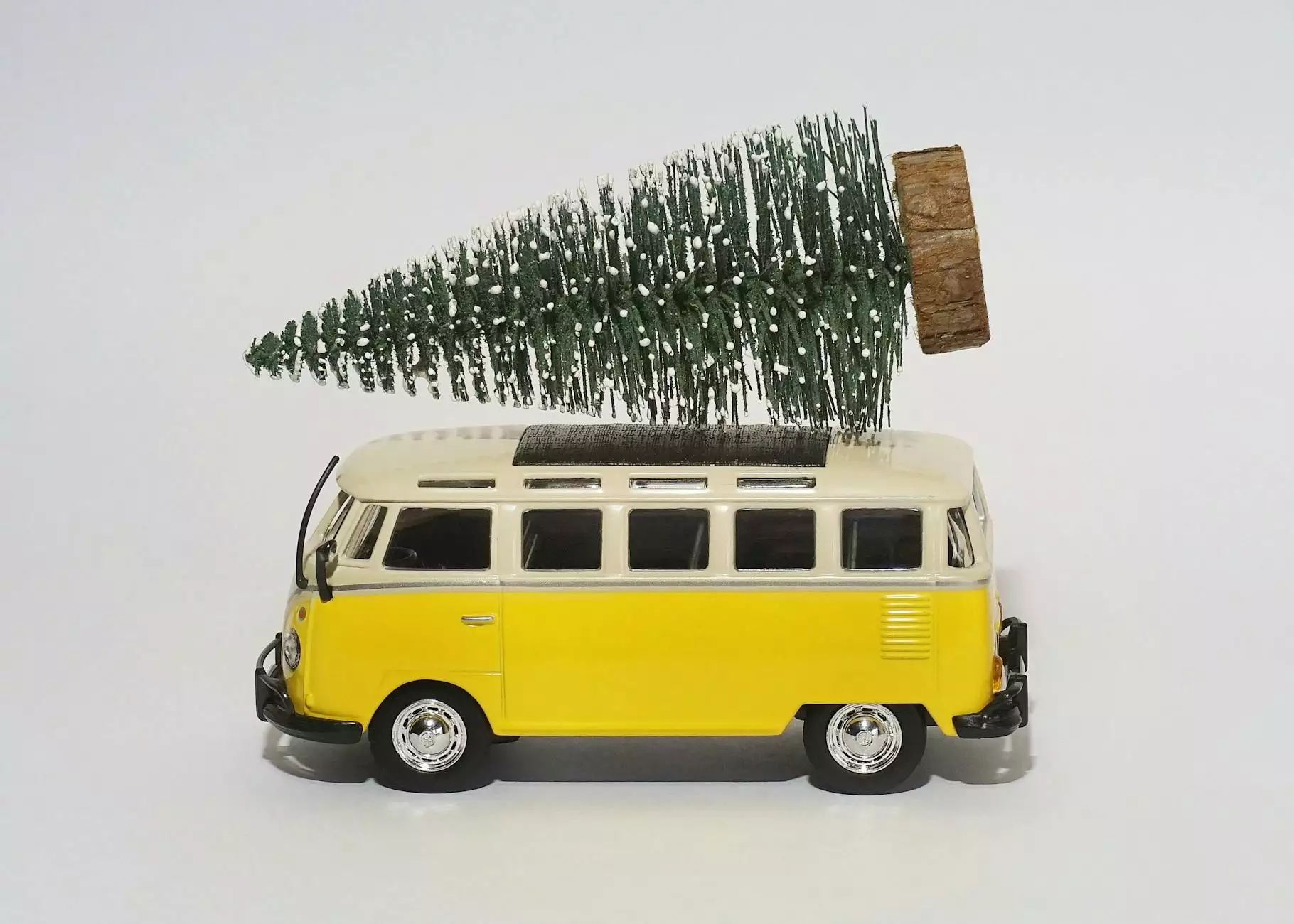
Die casting components manufacturers play a critical role in the production of high-precision metal parts across a wide array of industries. The die casting process is not just a manufacturing technique; it’s an essential method that enables companies to create complex shapes with outstanding accuracy and speed. In this extensive guide, we will delve into what die casting is, how it works, the benefits it brings, and why it is a preferred choice for manufacturers worldwide.
What is Die Casting?
Die casting is a metal casting process that involves forcing molten metal under high pressure into a mold cavity. This precision technique is widely utilized in producing intricate parts, making it a favorite among die casting components manufacturers.
Key Components of Die Casting
- Die: The mold used in the casting process, typically made from heat-resistant steel.
- Melting Furnace: Utilized to melt the metal material, usually aluminum, zinc, or magnesium.
- Injection Mechanism: The part that injects the molten metal into the die at high pressure.
- Cooling System: Allows the molten metal to solidify and take shape.
The Die Casting Process
The die casting process involves several critical steps that ensure the production of high-quality components. Below are the key stages of the process:
1. Die Preparation
The first step in the die casting process is preparing the die. The mold is thoroughly cleaned and coated with a release agent to facilitate the easy removal of the cast part after it cools.
2. Melting the Metal
Next, the chosen metal (commonly aluminum or zinc) is placed in a melting furnace, where it is heated until it reaches a molten state. This process must be closely monitored to ensure the metal is at the right temperature for injection.
3. Injection of Molten Metal
Once the metal is molten, it is injected into the die at high pressure. This step is crucial, as it allows the metal to fill every nook and cranny of the mold, creating highly detailed components.
4. Cooling and Solidification
After the molten metal is injected, it is allowed to cool and solidify. The cooling time can vary based on the thickness of the part being cast and the material used.
5. Ejection
Once the component has solidified, the die is opened, and ejector pins push the finished part out of the mold. The part is then ready for any necessary finishing processes.
Advantages of Die Casting
Die casting offers numerous advantages that contribute to its popularity among die casting components manufacturers:
- Precision and Accuracy: Die casting allows for tight tolerances, ensuring that parts fit together seamlessly.
- Complex Geometries: The process can create intricate shapes that are often difficult or impossible to achieve with other manufacturing methods.
- Material Efficiency: The process is highly efficient, leading to minimal waste of material.
- High Production Volumes: Die casting can produce large quantities of parts quickly, making it cost-effective for mass production.
- Enhanced Surface Finish: The resulting parts generally have a superior surface finish that often requires little to no further processing.
Common Applications of Die Casting
The versatility of die casting allows it to be utilized in various industries, each requiring different specifications and capabilities:
1. Automotive Industry
In the automotive industry, die casting is used to produce a vast array of components such as engine blocks, transmission cases, and various other structural parts. The durability and strength of die-cast parts make them ideal for automotive applications.
2. Consumer Electronics
Many consumer electronics rely on die cast components for their housings and internal structures. Because of the high precision required in electronic devices, die casting is often the best solution for manufacturers.
3. Aerospace
In aerospace, die casting is employed for parts that need to withstand extreme conditions while being lightweight. Components such as brackets and housings are common for die-cast production in this sector.
4. Household Appliances
Household appliances frequently use die casting for parts that require durability and efficiency, from kitchen equipment to larger appliances like refrigerators.
The Importance of Quality in Die Casting
Quality assurance in die casting is paramount. Die casting components manufacturers must adhere to strict standards to ensure that every component produced meets the necessary quality requirements.
Ensuring Quality Through Advanced Techniques
To maintain high-quality standards, manufacturers employ various techniques such as:
- Non-Destructive Testing (NDT): Used to identify internal defects without destroying the part.
- Spectrometer Analysis: To ensure the chemical composition of the metal is as specified.
- Dimensional Inspection: To verify that the finished parts meet tight tolerances.
Challenges Facing Die Casting Manufacturers
While die casting is a highly efficient and effective manufacturing process, it is not without its challenges. Understanding these challenges is crucial for improvement and innovation in the sector.
1. High Initial Setup Costs
One of the main challenges is the high initial cost of die setup. Although the cost per part decreases significantly with higher production volumes, new projects can be expensive.
2. Design Limitations
While die casting can produce complex shapes, there are still limitations regarding the shapes that can be manufactured. Components with sharp angles or deep cavities may require alternative fabrication methods.
3. Alloy Selection
Choosing the right alloy for the die casting process is critical. Different alloys offer various properties, and selecting the wrong one can lead to performance issues.
Future Trends in Die Casting
The die casting industry is continuously evolving. Understanding upcoming trends can provide valuable insights for manufacturers.
1. Increased Automation
Automation is set to play an even larger role in die casting, improving efficiency and reducing labor costs. Automated systems can ensure precise control and repeatability in the process.
2. Improved Materials
The development of new metal alloys and composites will expand the capabilities of die casting, allowing for improved performance characteristics.
3. Eco-Friendly Practices
As sustainability becomes more pressing, die casting manufacturers are looking for environmentally friendly practices, such as recycling materials and reducing waste during production.
Choosing the Right Die Casting Manufacturer
When selecting a die casting manufacturer, consider the following factors to ensure quality and reliability in your components:
- Experience: Look for manufacturers with a proven track record in die casting.
- Quality Assurance: Ensure the manufacturer follows rigorous quality control processes.
- Technological Capabilities: A manufacturer should utilize the latest technology to streamline processes.
- Customer Support: Good communication and after-sales support are essential for a successful partnership.
Conclusion
In conclusion, die casting components manufacturers are vital to various industries due to their ability to produce high-precision, complex parts efficiently. By embracing the advancements in technology and materials, these manufacturers can continue to meet the demanding standards of the market while paving the way for sustainable practices. As the industry evolves, staying informed about trends and challenges will be essential for businesses seeking to leverage die casting in their production processes.