Revolutionizing Metal Fabrication with Electric Injection Technology
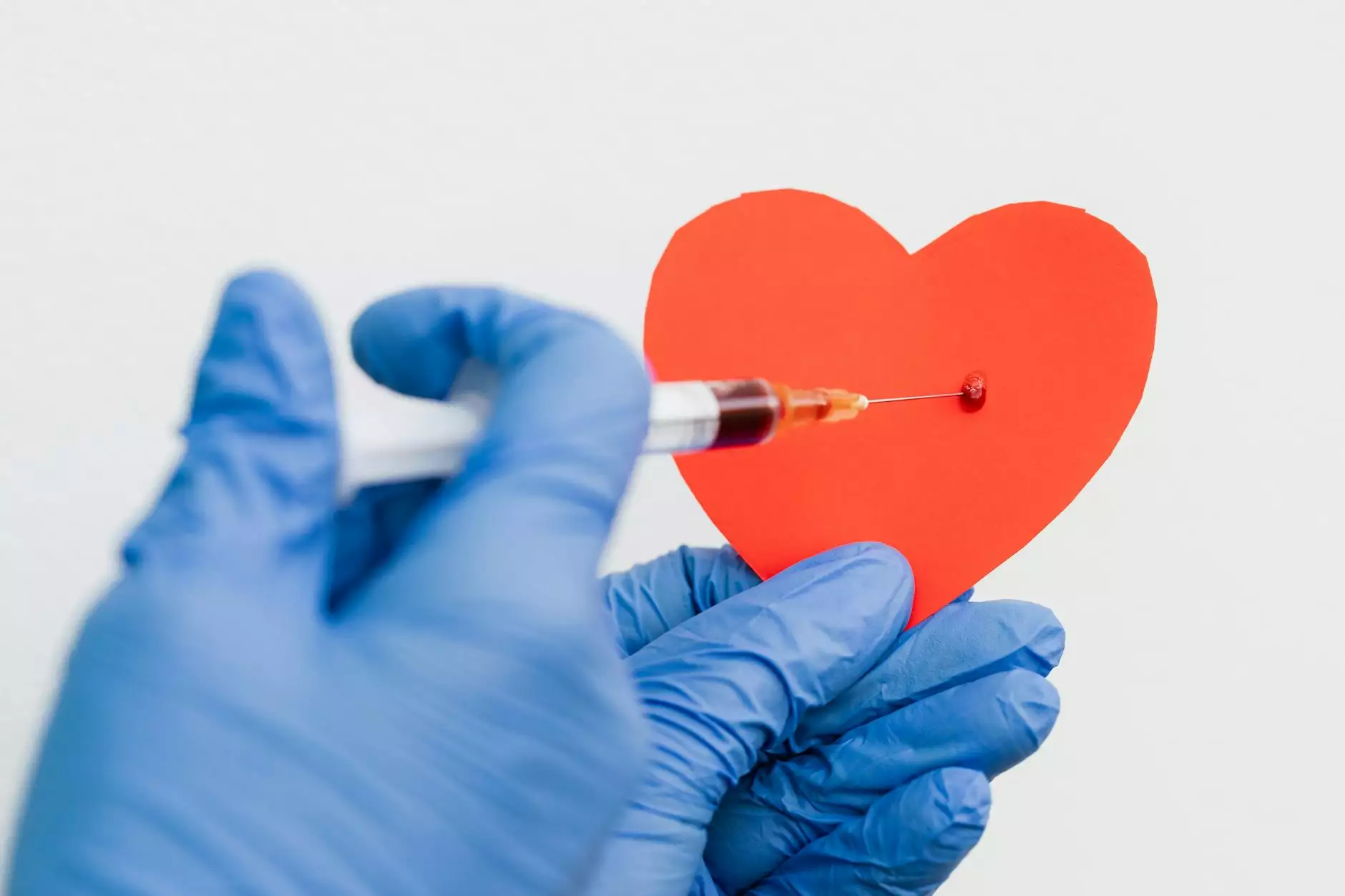
In the ever-evolving landscape of metal fabrication, companies are constantly seeking innovative technologies that enhance efficiency, precision, and sustainability. One such technological advancement making waves in the industry is electric injection. This article delves deep into the myriad ways electric injection is transforming the metal fabrication sector, the benefits it offers, and how businesses like DeepMould.net are leveraging this technology to stay ahead of the curve.
Understanding Electric Injection Technology
Electric injection refers to a modern process of injection that utilizes electric control systems to manage the injection and production of molten metal into molds. This technique, compared to its traditional counterparts, offers greater precision, enhanced energy efficiency, and improved environmental sustainability. Let’s explore the fundamental components of this technology.
The Mechanics Behind Electric Injection
- Precision Control: Electric injection systems use servo motors and advanced controllers to manage the speed and pressure of the injection process with unparalleled accuracy.
- Energy Efficiency: The transition from hydraulic to electric systems drastically reduces the energy consumption required for metal fabrication processes.
- Versatility: Electric injection can adapt to a variety of metals and alloys, making it suitable for numerous applications in different industries.
The Benefits of Electric Injection in Metal Fabrication
Incorporating electric injection technology into the metal fabrication process not only streamlines production but also offers several additional benefits:
1. Enhanced Production Speed
Electric injection systems are designed for faster cycle times, significantly reducing the time from raw material to finished product. This acceleration is driven by the rapid operation of electric servomotors, which can achieve quicker response times compared to traditional hydraulic systems.
2. Superior Precision and Quality
The ability to produce components with tight tolerances and reduced defects is a hallmark of electric injection technology. This precision ensures that every piece produced meets stringent quality standards, which is critical in applications requiring strict adherence to specifications.
3. Cost-Effectiveness
While initial investments in electric injection machinery may be higher, the savings in operational costs—due to reduced energy consumption, less maintenance, and improved yield—translate into long-term financial benefits.
4. Environmental Sustainability
Sustainable practices are increasingly essential in today’s industry. Electric injection systems produce fewer emissions and waste, making metal fabrication processes more eco-friendly. Additionally, the energy savings contribute to a smaller carbon footprint for manufacturing operations.
5. Improved Operator Safety
Electric systems can also enhance safety protocols within the production environment. Their streamlined operation reduces the risk of leaks or malfunctions associated with hydraulic systems, leading to a safer workplace.
Application of Electric Injection across Industries
The versatility of electric injection technology means it finds applications in various sectors. Here are a few examples of its widespread impact:
Aerospace Industry
With its emphasis on precision and reliability, the aerospace industry benefits significantly from electric injection technology. Components such as airframe parts, engine mounts, and intricate housing enclosures are often fabricated using this technology to ensure safety and performance.
Automotive Sector
The automotive sector embraces electric injection for producing lightweight, durable components. This includes everything from engine parts to detailed trim elements. The enhanced production speed ensures that manufacturers can keep pace with high consumer demand.
Electronics Manufacturing
In electronics, where precision is critical, electric injection allows for the secure production of housing and functional components that require meticulous detail and performance standards.
Medical Devices
For medical devices, the reliability of production and the ability to conform to stringent regulatory standards make electric injection indispensable. Applications range from surgical instruments to intricate implantable devices that require high precision and biocompatibility.
Challenges and Future Perspectives
Despite its advantages, the adoption of electric injection technology is not without challenges. Initial setup costs, the need for specialized training, and potential technological obsolescence can create barriers for some businesses. However, the long-term benefits and the ongoing trend towards automation and digitization make electric injection a worthy consideration for manufacturers.
The Road Ahead
As we look to the future, innovations in electric injection technology continue to evolve. The integration of artificial intelligence (AI) and machine learning with electric injection systems offers exciting potential for predictive maintenance, automated adjustments, and improved efficiency. Manufacturers like DeepMould.net are poised to take advantage of these innovations, leading the way in metal fabrication excellence.
Conclusion: Embracing the Future of Metal Fabrication
As industries strive for enhanced efficiency and sustainability, electric injection technology stands out as a transformative force in metal fabrication. By integrating this advanced technology, businesses can overcome production challenges, meet evolving market demands, and drive innovation within their operations.
The future of metal fabrication is bright, with electric injection at the forefront of this technological revolution. Companies that adopt this technology will likely benefit from improved capabilities, leading to enhanced competitiveness in a rapidly changing marketplace.
Call to Action
If you are interested in exploring how electric injection could benefit your metal fabrication needs, reach out to industry leaders like DeepMould.net. Together, we can unlock the full potential of your production capabilities and pave the way for a more efficient and sustainable future.