The Comprehensive Guide to Injection Molding Plastics
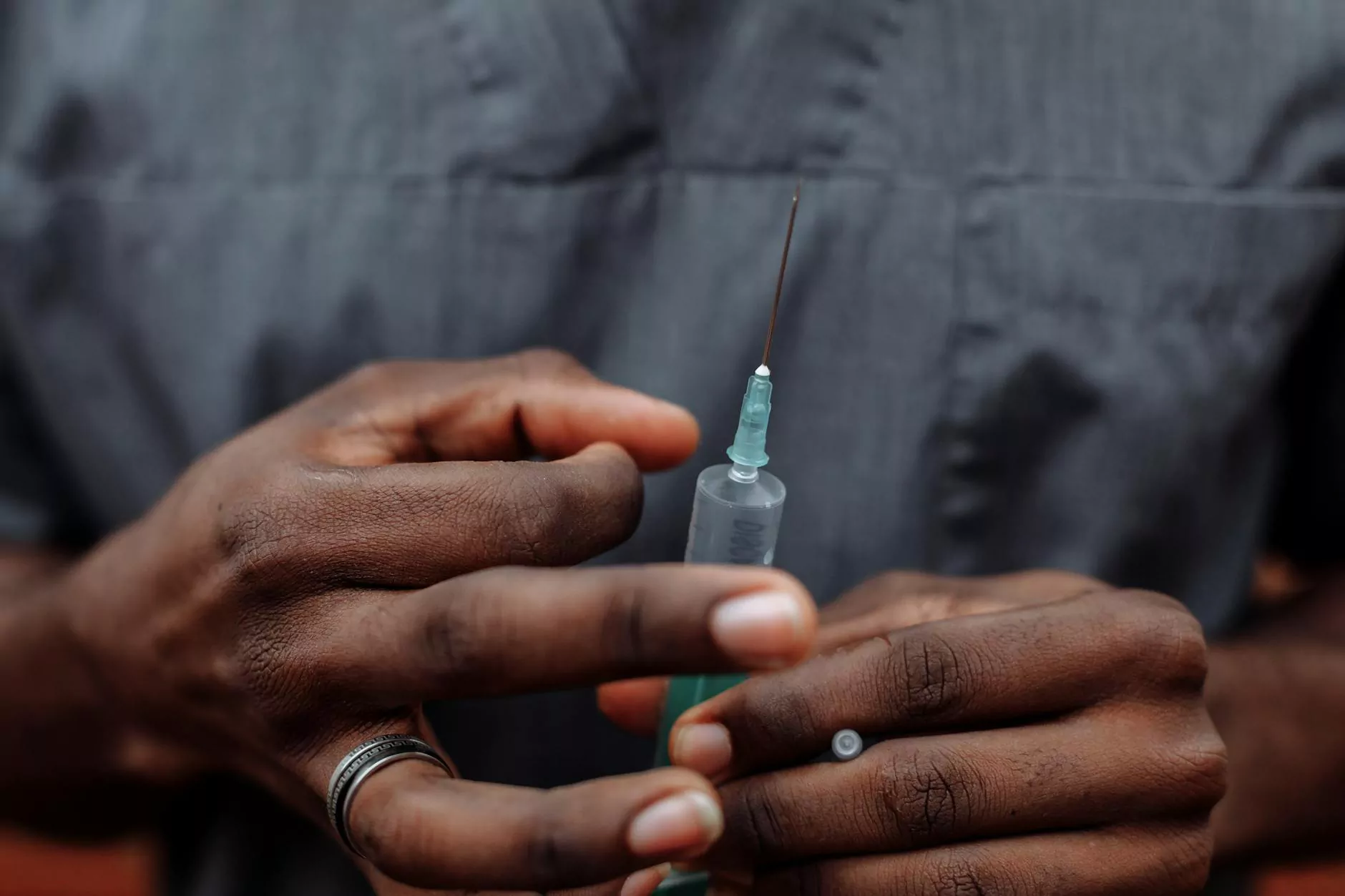
Injection molding plastics is a pivotal technology in modern manufacturing, enabling the mass production of intricate shapes and components with a high level of precision and efficiency. In this article, we will dive deep into the world of injection molding plastics, exploring its applications, processes, advantages, and its significant role in various industries, including metal fabrication.
What is Injection Molding?
Injection molding is a manufacturing process used to produce parts by injecting molten material into a mold. The materials commonly used in this process include various types of plastics, which are heated until they flow, then injected into a mold cavity to create the desired shape. Once the material cools, it solidifies and takes the shape of the mold.
The Injection Molding Process Explained
- Material Preparation: The process begins with the selection and preparation of the raw material. In most cases, this involves using granular plastic resins.
- Heating: The resins are fed into a heated barrel where they are melted and mixed to achieve a homogenous consistency.
- Injection: The molten plastic is injected into a precisely designed mold under high pressure. This step is crucial as it determines the dimensional accuracy of the final product.
- Cooling: After the plastic is injected, it needs time to cool and solidify within the mold. The cooling time depends on the material used and the size and complexity of the part.
- Ejection: Once the component has cooled sufficiently, the mold opens, and the part is ejected. This step marks the completion of the injection molding cycle.
Applications of Injection Molding Plastics
Injection molding plastics are utilized in a wide array of industries due to their versatility and efficiency. Here are some notable applications:
- Automotive Components: Dashboard parts, interior components, and various fixtures.
- Consumer Goods: Household items, packaging, and toys.
- Medical Devices: Syringes, surgical instruments, and diagnostic equipment.
- Electronics: Housings for devices, connectors, and insulators.
- Industrial Applications: Component parts for machinery and equipment.
Advantages of Injection Molding Plastics
The popularity of injection molding plastics can be attributed to several key advantages:
1. High Production Efficiency
Injection molding is capable of high-volume production runs, producing thousands of identical parts in a short period. This efficiency is crucial for businesses aiming to scale their production.
2. Precise Tolerances
The technology allows for tight tolerances and intricate designs, achieving a level of precision that is often unattainable through other manufacturing methods.
3. Material Versatility
With a broad range of plastic materials available, manufacturers can choose materials based on their specific needs, including those that offer enhanced properties such as temperature resistance, strength, and flexibility.
4. Minimal Waste
Injection molding is designed to produce parts with minimal waste, as the leftover material can often be reused in the process, making it a more sustainable manufacturing method.
5. Cost-Effectiveness for Larger Runs
While the initial setup costs can be high, the cost per part decreases significantly with larger production runs, making it economically favorable for mass manufacturing.
Choosing the Right Material for Injection Molding
When it comes to injection molding plastics, the choice of material can greatly influence the product's performance and cost. Here are some commonly used materials:
- Polypropylene (PP): Known for its chemical resistance and flexibility, commonly used in packaging and automotive parts.
- Polyethylene (PE): Very versatile, used for everything from bottles to pipe fittings.
- Polyvinyl Chloride (PVC): Widely used for plumbing, electrical wiring, and medical devices.
- Polystyrene (PS): Often used in disposable cutlery and packaging materials.
- ABS (Acrylonitrile Butadiene Styrene): Renowned for its durability and impact resistance, utilized in everything from LEGO bricks to automotive parts.
Injection Molding vs. Other Manufacturing Processes
To understand why injection molding plastics is so advantageous, it’s helpful to compare it with alternative manufacturing methods:
1. 3D Printing
While 3D printing allows for intricate designs and quick prototyping, it generally has slower production rates and may not be cost-effective for high volumes.
2. Blow Molding
This process is typically used for hollow objects and is less versatile when it comes to shapes compared to injection molding.
3. Compression Molding
Compression molding is suitable for larger parts but tends to be slower and less accurate than injection molding processes.
Quality Control in Injection Molding Plastics
Maintaining high quality in injection molding is vital for ensuring the reliability and safety of the end products. Quality control measures often include:
- Material Testing: Ensuring the chosen material meets industry standards.
- Dimensional Verification: Regularly measuring part dimensions to maintain precision.
- Visual Inspection: Identifying surface defects, color variations, and other cosmetic issues.
- Functional Testing: Conducting tests to ensure the part performs as intended in its application.
The Future of Injection Molding Plastics
The future of injection molding, particularly in plastics, appears promising, with several key trends shaping its evolution:
1. Technological Advancements
With ongoing innovations in machinery and processes, injection molding is becoming faster, more efficient, and increasingly precise. New materials are also being developed to expand the range of applications.
2. Sustainability Initiatives
As businesses aim to reduce their carbon footprints, there is a push towards using recycled materials and developing biodegradable plastics suitable for injection molding.
3. Industry 4.0
The integration of smart manufacturing techniques, including IoT and AI, is enhancing process monitoring, predictive maintenance, and overall operational efficiency in injection molding.
Conclusion: The Importance of Injection Molding Plastics in Modern Manufacturing
In summary, injection molding plastics plays a crucial role in the manufacturing landscape. Its efficiency, cost-effectiveness, and adaptability make it indispensable for a myriad of industries. As material science advances and manufacturing techniques improve, the potential for injection molding will continue to expand, further solidifying its importance in producing high-quality, reliable products.
For businesses operating in sectors like metal fabrication, recognizing the potential of injection molding plastics can open new avenues for innovative solutions, product development, and competitive advantages in the marketplace. By harnessing the capabilities of this technology, companies can ensure they remain at the forefront of manufacturing excellence.